Voices of the stakeholders
Interview with Dott. Luca Manuell
Chief Digital Officer & SVP Quality and IT and Process Improvement of Ansaldo Energia and President of the Italian Technological Cluster Intelligent Factory (CFI)
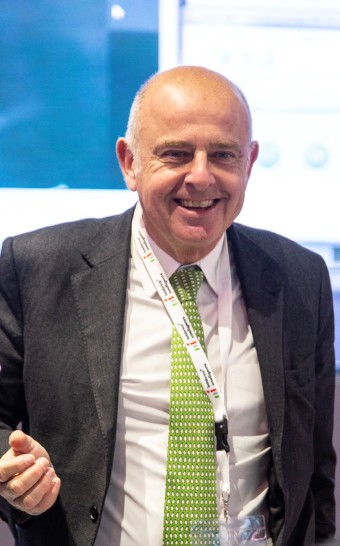
What about Lighthouse Plant and Ansaldo Energia?
The Factory of Ansaldo Energia in Genoa has been selected in 2018 by the Italian Technological Cluster Intelligent Factory (CFI) on behalf of the Ministry for Economic Development (MISE), as the first the Lighthouse Plant (LHP) of the Italian Enterprise Plan 4.0. Currently the network of the CFI Lighthouse Plant included 3 further key projects promoted by ABB, Tenova-ORI Martin and Hitachi Rail.
The digital transformation of Ansaldo Energia has been started many years ago and embraces all the key processes of its value chain, from product development increasingly integrated digitally with the service following a servizitation model, through production, supply chain management, construction and commissioning. Human Capital is constantly at the heart of Ansaldo Energia' digital transformation, in order to address technology to support a constant augmentation of the skills of our resources as well to improve work safety and healthy, along the overall Organization of the Group.
The Lighthouse Plant project scope include 8 application areas and a change management project effort aimed to transform Genoa Site into a data driven Factory, trough the digitization of production lines; the introduction of IoT Platforms to facilitate the collection, analysis and use of data to support decisions and actions; the introduction of Industry 4.0 technologies such as augmented and virtual reality, simulation and simplified human-machine interface to make production more flexible, agile and resilient. One of the experimental LHP goal supports the introduction of additive technology in the manufacturing process.
How Digital Manufacturing Can Mitigate the Impact of COVID-19?
The impact of collaboration between design, digital manufacturing and operations in a virtual environment has never been more beneficial. By leveraging 3D visualization and powerful optimization, companies like Ansaldo Energia in charge of high tech products can introduce the Digital Twin approach to virtually build products and target the "what," "where" and "how" will be manufactured. Digital solutions that demonstrate that companies are operational and able to take orders and respond to requests are in high demand.
In Phase 2 of Covid19, the factory is becoming the protagonist of the research to identify the technologies suitable to push the innovation of Italian Manufacturing, redefining industrial processes in an innovative key from production to distribution. Carrying on the Lighthouse Plant project at this difficult time is an example of how the country system, represented by the world of research and large, medium and small businesses, when teaming up can confidently face the challenges of the global economy creating value for the overall economic system. In particular Ansaldo Energia boosted the deployment of Smart Safety application extended to face the COVID emergency leveraging on the investment already launched to introduce sensors and IoT platform to support the safety of our workers. The Lighthouse Plant is a fantastic demonstrator of how, by applying digital technology, you get benefits.
Why do manufacturing companies need to implement culture in the field of additive manufacturing?
Manufacturing companies can address three main areas of benefit from the introduction of Additive Manufacturing; in particular:
a. the possibility to redesign components and parts of turbines for additive with shapes which enable performances technically and economically not sustainable with the traditional approach. Main benefits in this area can be time-to-market through the reduction of lead times (from months to hours) as well as performance and quality improvements). AM can also support the servitization process through the introduction of smart material which enable sensors to collect data from the running turbine useful to the deployment of new predictive maintenance added value services;
b. the introduction of AM in repair process which can support the extension of the product lifecycle. The new flexible Intelligent Factory shall be more and more asked to support different needs coming from the New Units (Turbines and Power Plants) and the Service market and AM is a key technology to support such dual mission;
c. the possibility to empower field service activities and redesign the supply chain by the introduction of the on-site Additive Manufacturing process to produce spare parts to optimize the working capital and also to achieve time-to-market benefits coming from the new predictive maintanance application supported from remote by the use of AR/VR devices.
What was one of the most important experiences in the AM field at Ansaldo Energia?
One of the most important experimental activities in the field of additive, is part of one of the objectives, named "Hot Gas Part Components Repair" and is carried out in collaboration with the Joint Laboratory Genoa Additive Manufacturing (GeAM) of Additive Manufacturing and 3D printing result of the agreement signed between the Italian Institute of Welding and the Polytechnic School of the University of Genoa with the departments of Mechanical Engineering, Energy, Management and Transport (DIME) and Civil Engineering, Chemistry and Environmental (DICCA), both departments actively involved in AMiCE project.
To date, AEN additive production is carried out by suppliers who have reached a certain technological maturity. This project is a great opportunity for AEN to consolidate, control and share AM knowledge and define a more stringent qualification path for Suppliers. In this case we are talking about laser additive manufacturing technology with Powder Bed Fusion. A company's know-how must always be measured by the culture and experience of academia and the involvement in sharing culture around the AM and Circular Economy topics promoted by AMiCE alliance and network is a great opportunity.
Why should this project be done and why now?
In the last years, Industry 4.0 has been considered one of the most strategic lever to support the increase of competitiveness of our country and has gained significant popularity both in academia and the manufacturing sector.
In such frame, Additive Manufacturing has become one of the leading technologies in the framework of Industry 4.0 with various applications in key industrial sectors such as power generation. It should be done because the times of digital standardization are extremely fast and therefore it is better to anticipate change as soon as possible to keep up with technology and overcome the barriers of an increasingly dynamic market. It must be done now because the time has come to better evaluate our company's Technology Readiness Level (TRL) in the field of additive to have under control the production process of our suppliers and consequently the quality of our components.
The collaboration between AEN and the University – and hence AMiCE network – through a continuous exchange of knowledge in support of this experimental project, becomes of strategic importance for the innovation and development of our company.
More information:www.ansaldoenergia.com