Waste heat utilization in European energy intensive industries
6.9.2017
1. INTRODUCTION
During the industrial processes (steel mills, paper plants, refineries, chemical plants, oil and gas pipelines, and general manufacturing, etc.) heat is generated as a by-product. Experts consider the dissipation of waste heat to the atmosphere as a wasted opportunity if it is not reused. Some studies estimated that about 20-50% of the industrial energy consumption is discharged as heat [1].
The Waste Heat to Power (WHP) process is to use recovered waste heat in order to generate electricity without any combustion or emission. These systems use the technology that is the same as with solar or geothermal energy systems. They capture heat at the surface and convert it into electricity. Nevertheless, waste heat to power is often ignored and underdeveloped. Recently, newer techniques proved in the solar and geothermal industry that they are capable of capturing waste heat even in a smaller scale and at lower temperatures. The constantly invented developments are creating new opportunities to capture heat and convert it to useful power. Due to the application of these techniques waste heat is now a resource for emission-free electricity, like other renewable resources [2].
A substantial amount of heat is wasted in numerous industrial plants employing thermal processes. Waste heat recovery methods have shown a great development since many years. Depending on the application, the heat can be the desired product or can be the input to another process to generate clean electricity as mentioned above. In case a certain quantity and quality of waste heat is available, it is recommended to invest to some kind of heat utilization facility, for instance Organic Rankine Cycle (ORC), which is profitable for both the investor and its environment. In the last ten years many ORC turbines have been installed to benefit from the heat from cement kilns, metallurgy processes, gas turbines or internal combustion engines. Companies who invested to such turbines successfully reduced their electricity consumption without using any additional primary energy. In 2010 the mapping of the potential for heat recovery with ORC systems in energy intensive industries started. An evaluation was carried out at European level of the potential electricity generation with this technology. An estimation was made which states that the theoretical potential of ORC gross power is about 2.5 GW. Considering 8000 operating hours (this is dependent on the market fluctuations) these plants can generate about 20TWh of electric energy which is 4.8% of total electricity consumption of EU industry in 2009. Calculating with these numbers it may result in the avoided emission of 7.5 million tonnes of carbon dioxide [3].
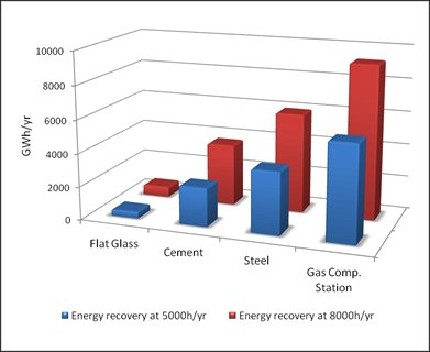
Figure 1: Annual energy recovery in EU27 industries in 2009 [3]
2. WASTE HEAT RECOVERY IN EU27 CEMENT PLANTS, STEEL PLANTS, GLASS PLANTS, GAS COMPRESSOR STATIONS: ESTIMATE ON ORC POWER
According to a survey [3] over 576 MW of ORC power can be installed in EU27 cement industry. Calculating with 5000 and 8000 operating hours per year, the annual energy recovery in this industry would be 2.87 and 4.59 TWh from waste heat. The avoided emission of CO2 is about 1.5 million metric tons in 2010 by EU27 industry.
Electric Arc Furnaces (EAFs) and rolling mills are considered to be the most suitable for ORC applications to recover waste heat in the steel sector. It has been estimated [3] that the annual power generation from waste heat recovery is between 3740 and 5984 GWh. This is about the 0.58% of the final electricity consumption of EU27 industry in 2007. The avoided CO2 emissions are between 1.351 and 2.162 million tonnes.
Considering only flat glass plants (it was not possible to get access to every glasswork`s database) we can state the total number of such plants in EU27 is 58. The total gross ORC power is 75.5 MW and the energy generation from waste heat recovery is estimated from 392.6 GWh to 628.2 GWh per year implying a decrease in CO2 emission by 140333 tonnes (5000 hours/year) and 224533 tonnes (8000 hours/year) [3].
In UE27 countries 1304 MW ORC gross power can be installed generating up to 10.43 TWh per year electricity. This way 3.7 million metric tons of green house gas can be avoided [3].
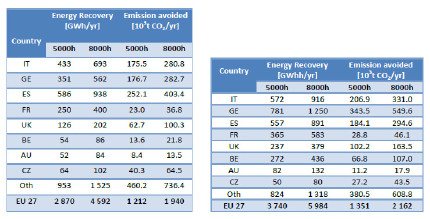
Table 1 and 2: Power generated from waste heat recovery and emission savings in the cement (2010) and steel industry (2007) [3]
3. CONCLUSIONS
Waste heat is now a resource that can be utilized or discarded. In the industrial sector the use of its energy can be outstandingly beneficial for different actors and the environment.
Europe has a leading role in developing low-carbon and energy efficiency solutions, moreover, heat recovery can help the EU to reach the objective of 20% reduction in energy consumption. Besides the obvious benefit of decarbonisation and sustainable growth, the use of WHR applications would contribute to job creation, the improvement of the Resource & Development sector and have a positive effect to productivity and competitiveness. In order to put into effect these benefits EU should consider some measures to make a good environment for such investments. These measures could consist of three pillars: a new, energy efficiency directive, EU supported specific provision to finance waste heat recovery power generation to shorten the investment payback period, and increased awareness through dissemination (proper education and trainings) campaigns. If the ideas of these pillars manage to come true, that might mean a huge step towards sustainable development and a better future [3].
References:
[1]. BCS, Incorporated: Waste Heat Recovery: Technology and Opportunities in U.S. Industry, 2008
[2]. Heat is Power: www.heatispower.org, 12.12.2016
[3]. EU paper: ORC Waste Heat Recovery in European Energy Intensive Industries